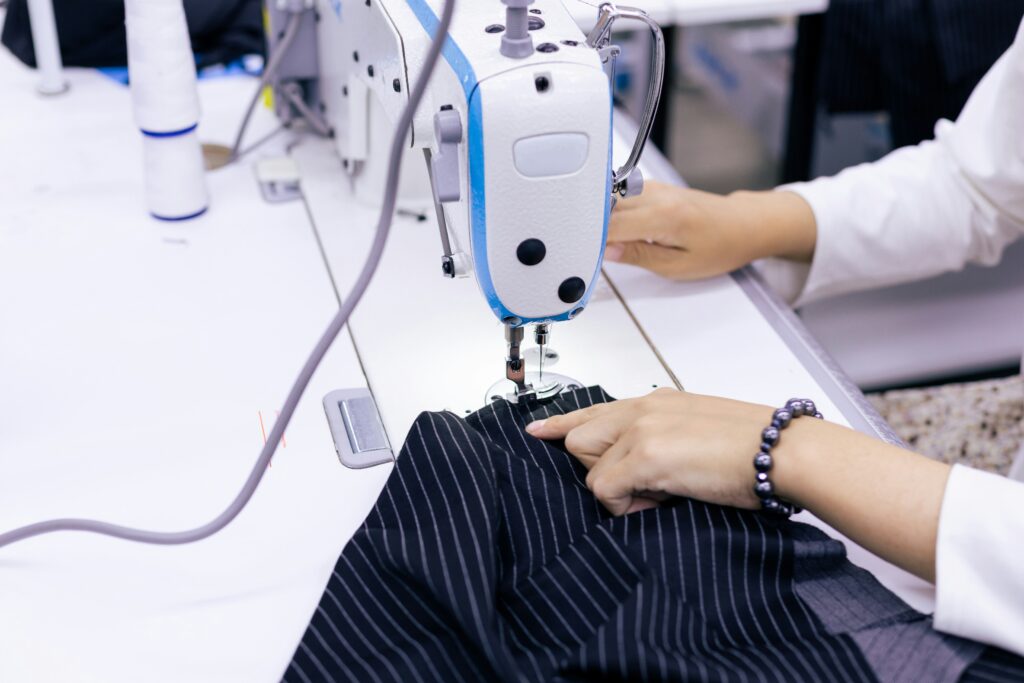
Top 15 Apparel Manufacturing Mistakes to Avoid for Quality and Efficiency.
In the fast-paced world of apparel manufacturing, staying ahead of the competition while maintaining high-quality standards is crucial. Whether you’re a seasoned manufacturer or just starting in the industry, avoiding common pitfalls can make the difference between success and failure. This comprehensive guide will walk you through the top 15 apparel manufacturing mistakes that can impact your quality and efficiency, and provide actionable tips to overcome them.
By addressing these issues, you’ll be able to streamline your production process, reduce costs, and deliver superior products to your customers. Let’s dive into the most critical mistakes to avoid in apparel manufacturing and how to overcome them.
1. Poor Fabric Selection and Quality Control
One of the most fundamental aspects of apparel manufacturing is choosing the right fabric. Selecting low-quality materials or failing to properly inspect them can lead to numerous issues down the production line.
Common mistakes:
• Choosing fabrics based solely on cost without considering durability and performance
• Neglecting to test fabric samples for colorfastness, shrinkage, and pilling
• Failing to inspect incoming fabric rolls for defects or inconsistencies
How to avoid:
• Establish strict quality control measures for fabric selection and inspection
• Conduct thorough testing of fabric samples before bulk ordering
• Work closely with reliable suppliers who consistently provide high-quality materials
• Implement a fabric grading system to ensure only the best materials make it to production
2. Inaccurate Pattern Making and Grading
Patterns are the foundation of garment construction. Errors in pattern making or grading can result in ill-fitting garments and increased production costs.
Common mistakes:
• Rushing through the pattern-making process without proper testing
• Failing to account for fabric properties when creating patterns
• Inconsistent grading across size ranges
How to avoid:
• Invest in skilled pattern makers and up-to-date pattern-making software
• Create and test multiple prototypes before finalizing patterns
• Develop a standardized grading system that accounts for different body types and fabric characteristics
• Regularly review and update patterns based on customer feedback and industry trends
3. Inefficient Cutting Processes
Cutting is a critical step in apparel manufacturing that can significantly impact material waste and production efficiency.
Common mistakes:
• Improper fabric spreading techniques leading to misaligned layers
• Inefficient marker making resulting in excessive fabric waste
• Using dull or inappropriate cutting tools for different fabric types
How to avoid:
• Implement automated spreading and cutting systems for increased accuracy and efficiency
• Optimize marker making with advanced software to minimize fabric waste
• Regularly maintain and replace cutting tools to ensure clean, precise cuts
• Train cutting room staff on proper techniques for handling different fabric types
4. Overlooking Proper Garment Construction Techniques
The construction phase is where individual pieces come together to form a finished garment. Neglecting proper techniques can lead to quality issues and increased returns.
Common mistakes:
• Inconsistent seam allowances and stitch lengths
• Improper use of interfacing and stabilizers
• Neglecting to reinforce stress points in garments
How to avoid:
• Develop detailed construction guidelines for each garment type
• Provide ongoing training for sewing operators on proper techniques
• Implement quality checks at various stages of the construction process
• Use appropriate interfacing and stabilizers to enhance garment structure and durability
5. Inadequate Quality Control Measures
Quality control is essential throughout the manufacturing process. Failing to implement robust QC measures can result in defective products reaching customers.
Common mistakes:
• Relying solely on end-of-line inspections
• Inconsistent quality standards across different production lines or facilities
• Lack of clear communication regarding quality expectations
How to avoid:
• Implement a comprehensive quality management system covering all stages of production
• Conduct regular in-process inspections and audits
• Establish clear quality standards and communicate them effectively to all team members
• Utilize statistical process control techniques to identify and address quality issues proactively
6. Poor Time Management and Production Planning
Efficient production planning is crucial for meeting deadlines and maintaining consistent quality. Poor time management can lead to rushed production and increased errors.
Common mistakes:
• Underestimating production times for complex garments
• Failing to account for potential delays in material sourcing or equipment maintenance
• Overcommitting to orders without considering production capacity
How to avoid:
• Utilize production planning software to optimize workflow and resource allocation
• Develop realistic timelines that account for potential setbacks
• Implement a robust capacity planning system to balance orders with production capabilities
• Regularly review and adjust production schedules based on real-time data and feedback
7. Neglecting Sustainable Practices
With increasing focus on sustainability in the fashion industry, neglecting eco-friendly practices can harm your brand reputation and limit market opportunities.
Common mistakes:
• Disregarding environmental impact of production processes
• Failing to explore sustainable material options
• Overlooking opportunities for waste reduction and recycling
How to avoid:
• Implement sustainable production practices, such as water and energy conservation
• Explore eco-friendly fabric options and innovative sustainable materials
• Develop a waste management strategy that includes recycling and upcycling initiatives
• Obtain relevant sustainability certifications to demonstrate commitment to eco-friendly practices
8. Ineffective Communication with Suppliers and Clients
Clear communication is vital for ensuring that products meet specifications and deadlines. Misunderstandings can lead to costly mistakes and delays.
Common mistakes:
• Failing to provide clear, detailed specifications to suppliers
• Inadequate communication of changes or revisions to production teams
• Neglecting to keep clients informed about production progress or potential issues
How to avoid:
• Develop comprehensive tech packs and specification sheets for each product
• Implement a centralized communication system for sharing updates and revisions
• Schedule regular check-ins with suppliers and clients to address concerns and provide updates
• Utilize collaborative tools and platforms to streamline communication across all stakeholders
9. Inadequate Employee Training and Development
Well-trained staff are essential for maintaining quality and efficiency in apparel manufacturing. Neglecting employee development can lead to increased errors and reduced productivity.
Common mistakes:
• Providing minimal training for new employees
• Failing to keep staff updated on new technologies and techniques
• Neglecting to cross-train employees for different roles
How to avoid:
• Develop comprehensive training programs for all aspects of apparel manufacturing
• Offer ongoing professional development opportunities to keep staff skills up-to-date
• Implement a mentoring system to facilitate knowledge transfer between experienced and new employees
• Encourage cross-training to improve flexibility and understanding of the entire production process
10. Overlooking Proper Equipment Maintenance
Well-maintained equipment is crucial for consistent quality and efficient production. Neglecting maintenance can lead to unexpected breakdowns and quality issues.
Common mistakes:
• Failing to schedule regular maintenance checks
• Neglecting to clean and calibrate equipment regularly
• Delaying repairs or replacements of faulty equipment
How to avoid:
• Implement a preventive maintenance schedule for all equipment
• Train operators on proper equipment care and basic troubleshooting
• Keep detailed maintenance logs and analyze data to identify potential issues before they occur
• Invest in modern, efficient equipment to improve productivity and reduce maintenance needs
11. Inefficient Inventory Management
Poor inventory management can lead to stockouts, overstock situations, and increased carrying costs, all of which impact efficiency and profitability.
Common mistakes:
• Inaccurate demand forecasting leading to excess inventory or shortages
• Inefficient storage and organization of materials and finished goods
• Lack of real-time inventory tracking across multiple locations
How to avoid:
• Implement an advanced inventory management system with real-time tracking capabilities
• Utilize data analytics for more accurate demand forecasting
• Optimize warehouse layout and storage systems for efficient material flow
• Regularly conduct physical inventory counts to ensure accuracy of digital records
12. Neglecting Compliance and Safety Standards
Failing to adhere to industry regulations and safety standards can result in legal issues, fines, and damage to your brand reputation.
Common mistakes:
• Overlooking local and international labor laws and regulations
• Failing to implement proper safety measures in production facilities
• Neglecting to obtain necessary certifications for specific markets or product types
How to avoid:
• Stay informed about relevant industry regulations and standards
• Conduct regular safety audits and implement necessary improvements
• Provide comprehensive safety training for all employees
• Work with compliance experts to ensure adherence to all applicable regulations
13. Inadequate Cost Control Measures
Effective cost management is crucial for maintaining profitability in the competitive apparel manufacturing industry.
Common mistakes:
• Failing to accurately calculate and monitor production costs
• Overlooking opportunities for process optimization and cost reduction
• Neglecting to negotiate favorable terms with suppliers
How to avoid:
• Implement a robust cost accounting system to track all production-related expenses
• Regularly analyze production processes to identify areas for cost reduction and efficiency improvements
• Develop strong relationships with suppliers and negotiate volume-based discounts
• Explore opportunities for vertical integration to reduce reliance on external suppliers
14. Neglecting Product Development and Innovation
In the fast-paced fashion industry, failing to innovate can lead to stagnation and loss of market share.
Common mistakes:
• Relying too heavily on existing product lines without exploring new designs
• Failing to invest in research and development of new materials and technologies
• Neglecting to gather and incorporate customer feedback into product development
How to avoid:
• Allocate resources for ongoing research and development initiatives
• Stay informed about emerging trends and technologies in the apparel industry
• Actively seek and incorporate customer feedback into the product development process
• Collaborate with designers and textile innovators to create unique, market-driven products
15. Poor Data Management and Analysis
In today’s data-driven world, failing to effectively collect, manage, and analyze production data can hinder continuous improvement efforts.
Common mistakes:
• Relying on manual data collection and analysis methods
• Failing to integrate data from different stages of the production process
• Neglecting to use data insights for strategic decision-making
How to avoid:
• Implement an integrated Manufacturing Execution System (MES) to collect real-time production data
• Utilize advanced analytics tools to identify trends, bottlenecks, and improvement opportunities
• Train staff on data-driven decision-making processes
• Regularly review key performance indicators (KPIs) and adjust strategies accordingly
Avoiding these top 15 apparel manufacturing mistakes is crucial for maintaining high quality standards and operational efficiency. By addressing these common pitfalls, you can streamline your production processes, reduce costs, and deliver superior products to your customers.
Remember that continuous improvement is key in the dynamic apparel manufacturing industry. Regularly assess your operations, stay informed about industry trends, and be willing to adapt your processes to maintain a competitive edge.
By implementing the strategies outlined in this guide, you’ll be well-positioned to overcome common challenges and achieve success in the apparel manufacturing sector. Keep innovating, prioritize quality, and always strive for excellence in every aspect of your production process.
Are you ready to take your apparel manufacturing to the next level? Implement these strategies in your operations and see the difference in quality and efficiency. Share your experiences or ask for more advice in the comments below. Don’t forget to subscribe to our blog for more insights into apparel manufacturing best practices!